We craft custom bushings from solid lubricants, and sintered metals, optimizing performance for your specific environment.
DAEKEUM GEOWELL's high-quality non-ferrous bushings enhance equipment performance across diverse industries.
Choose the right bushing for your application.
OILLESS BUSHING
Model : GOL
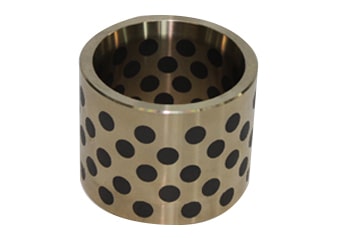
Graphite Plugged Brass Bushing incorporates high quality copper alloy metals with special solid lubricant plugs. The fine particles of solid lubricant makes superb self lubrication and abrasion resistance possible.
Graphite Plugged Brass Bushing shows good performance in high and low temperature and shows excellent corrosion resistance and chemical resistance, so it can be used under water or inside of chemical process.
This model is suitable to be used in circumstances of heavy load, low speed, reciprocating motion, oscillating motion and intermittent movement.
Technical specifications
Type | GOL |
---|---|
Material | #500SP |
Pressure | Max.100 Mpa |
Speed | Max. 0.5 m/s |
PV value | 1.8MPa.m/s |
Temperature | Max.300°C |
Lubrication | Grease |
Friction Coefficient | 0.12 ~ 0.16 |
Hardness | HB 180 ~ 230 |
Greasing Interval | 500hours |
Features of Relative Shafts
- In order to achieve optimal performance of pin joint, the surface roughness under 0.8μm(∇∇∇) is recommended.
- Considering abrasion and impact strength, the surface hardness is recommended to be between HRc 55 ~ 60.
SINTERED BUSHING
Model : GSN
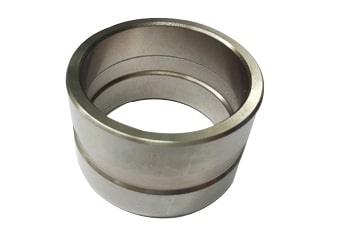
Sintered Bushing has superb load resistance and abrasion resistance and is recommended to be used in low-speed and heavy-load circumstance.
Sintered Bushing is composite bearing which impregnates the high-viscosity oil and is used in places where supplying lubricant is not easy.
Technical specifications
Type | GSN |
---|---|
Material | Steel based metal powder |
Pressure | Max.75 Mpa |
Velocity | Max. 1.0 m/s |
PV value | 2.0MPa.m/s |
Temperature | Max.150°C |
Lubrication | Grease |
Friction Coefficient | 0.14 ~ 0.18 |
Lubricant supply interval | 1000hrs |
Features of Relative Shafts
- In order to achieve optimal performance of pin joint, the surface roughness under 0.8μm(∇∇∇) is recommended.
- Considering abrasion and impact strength, the surface hardness is recommended to be between HRc 55 ~ 60.